Understanding PTFE Flexible Hose Manufacturing A Comprehensive Overview
Polytetrafluoroethylene (PTFE), commonly known as Teflon, is a highly versatile material with exceptional chemical resistance and temperature stability. Its flexibility makes it an ideal choice for manufacturing hoses that cater to various industrial applications. This article delves into the world of PTFE flexible hose factories, exploring their operations, manufacturing processes, and the significance of these products in modern industries.
PTFE flexible hose factories are specialized facilities that produce hoses designed to withstand harsh environments and demanding conditions. These hoses find extensive use in sectors such as chemical processing, pharmaceuticals, food and beverage, automotive, and aerospace, among others. The primary advantage of PTFE hoses lies in their ability to maintain their integrity and functionality even at extreme temperatures, ranging from -73°C (-99°F) to 260°C (500°F).
The manufacturing process begins with the selection of high-quality PTFE resin. This raw material is then transformed into a dough-like consistency through a process called cold-working or calendaring. The PTFE dough is then formed into a tube shape, which is either extruded or braid-reinforced for added strength and flexibility.
Extrusion involves forcing the PTFE resin through a die to create a continuous tube. The resulting hose is then heat-treated or annealed to stabilize its molecular structure. On the other hand, braid reinforcement involves weaving a wire or fabric around the PTFE tube, enhancing its pressure and burst ratings. This step is crucial for applications that require high-pressure resistance This step is crucial for applications that require high-pressure resistance
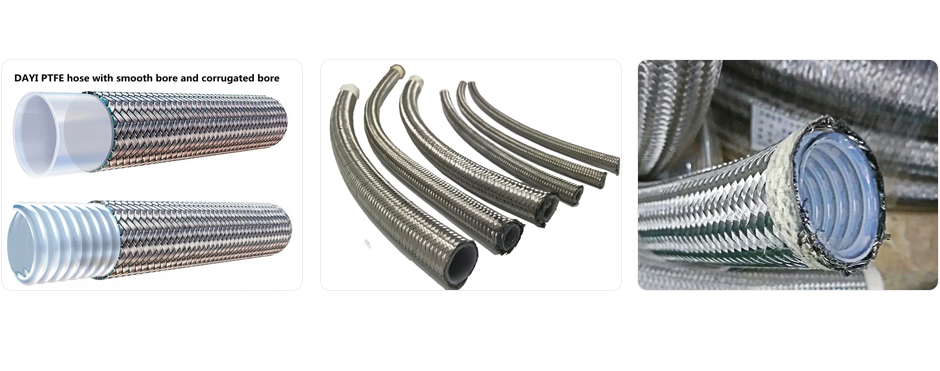
This step is crucial for applications that require high-pressure resistance This step is crucial for applications that require high-pressure resistance
ptfe flexible hose factories.
Once the hoses are manufactured, they undergo rigorous quality control checks to ensure compliance with industry standards. This includes testing for pressure resistance, flexibility, chemical compatibility, and dimensional accuracy. The finished products are then packaged and distributed to meet the diverse demands of global markets.
PTFE flexible hoses offer numerous benefits, including chemical inertness, non-stick surface, excellent electrical insulation, and low friction. Their unique properties make them indispensable in industries where safety, durability, and reliability are paramount. For instance, in chemical plants, PTFE hoses prevent chemical reactions with the hose material, ensuring safe transportation. In the food industry, they meet strict hygiene requirements due to their non-toxic nature.
In conclusion, PTFE flexible hose factories play a vital role in providing essential components for a wide range of industries. They leverage advanced technologies and stringent quality control measures to manufacture hoses that can withstand the toughest conditions. As technology continues to evolve, these factories will undoubtedly continue to innovate, producing more efficient and specialized PTFE hoses to meet the ever-changing needs of industries worldwide.