Natural gas hoses are critical components in the energy supply chain, facilitating efficient and safe transportation of natural gas from one point to another. As an industry expert with years of experience and deep technical knowledge, I will delve into what makes a natural gas hose factory a significant player in the market. This article highlights the meticulous process involved in manufacturing natural gas hoses, the quality standards upheld, and the features that ensure safety and reliability.
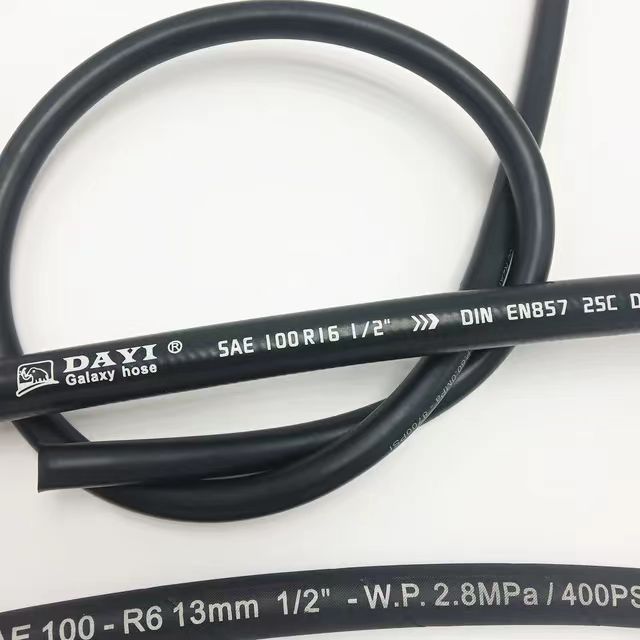
In a world where sustainable energy solutions are paramount, factories producing natural gas hoses serve as vital hubs for meeting global energy demands efficiently. Such factories integrate state-of-the-art technology with stringent safety measures to produce high-quality hoses capable of sustaining high pressure and harsh environmental conditions.
Expertise in the field is demonstrated through the careful selection of materials, which must possess exceptional durability and resistance to corrosion and abrasion. Natural gas hose factories typically employ a combination of advanced polymers and engineered reinforcements, tailored specifically to transport natural gas safely. These materials undergo rigorous testing to withstand various pressures and temperatures, ensuring compliance with industry standards, such as ASTM and ISO certifications.
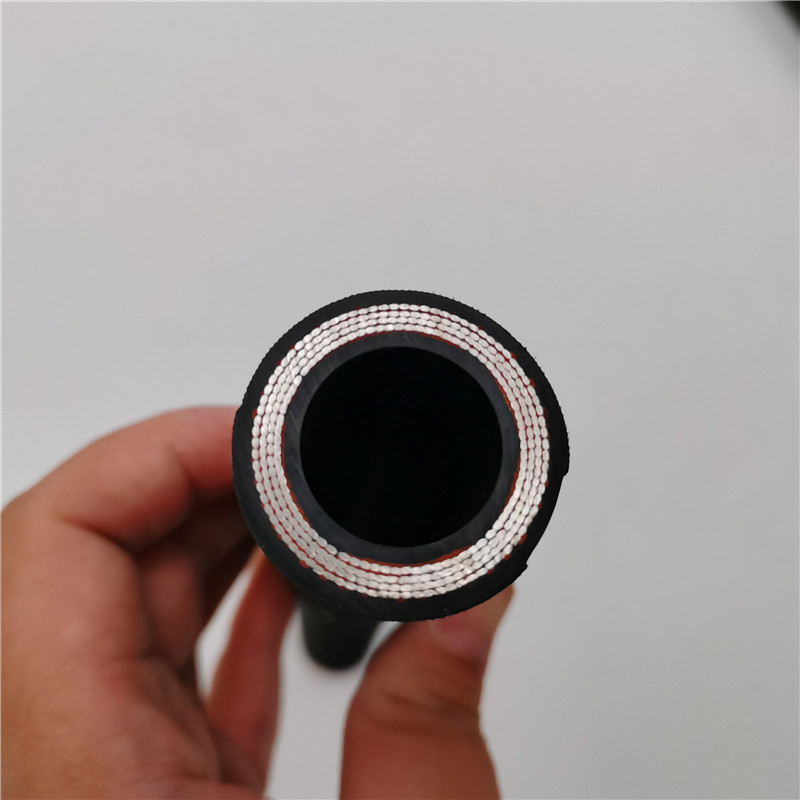
The manufacturing process begins with the design phase, where engineers use cutting-edge software to develop hose prototypes that meet specific industrial needs. Precision in design is crucial, as it ensures the finished product delivers optimal performance and longevity. The production line itself is a symphony of automation and craftsmanship, where sophisticated machinery and skilled technicians work in harmony to fabricate hoses that adhere to exacting specifications.
Another key aspect of these factories is their commitment to research and innovation. Continuous improvement initiatives are rooted in scientific expertise, focusing on enhancing the efficiency and environmental sustainability of natural gas hoses. This dedication to innovation is what sets some factories apart as industry leaders and is a testament to their authority in the field.
natural gas hose factory
Trustworthiness is further established through transparent quality assurance processes. Each hose produced undergoes comprehensive inspections and testing, such as hydrostatic tests, bend tests, and leak tests, to confirm its integrity and safety. Furthermore, reliable factories often provide detailed product documentation, offering customers insights into the hose's lifecycle, maintenance requirements, and safety guidelines.
These factories also build trust through robust partnerships with suppliers and clients, fostering relationships based on reliability and openness. A reputable natural gas hose factory will engage in regular consultations with clients, tailoring products to specific needs, and providing technical support and training on product use and maintenance.
Finally, the ethos of a high-caliber natural gas hose factory revolves around its workforce's expertise. The emphasis on workforce training programs and safety protocols ensures that all personnel are well-versed in contemporary techniques and industry standards. By equipping employees with advanced skills and knowledge, these factories not only enhance their operational effectiveness but also contribute to a culture of safety and excellence.
In conclusion, a natural gas hose factory represents more than just a production facility. It is a beacon of quality and reliability, founded on the pillars of experience, expertise, authoritativeness, and trustworthiness. The dedication to these principles not only benefits the immediate industry but also contributes to a broader commitment to safe and sustainable energy solutions globally.