In the world of manufacturing, particularly within the niche of LPG gas hose production, certain qualities distinguish the noteworthy from the merely adequate. The journey of transforming raw materials into reliable, high-quality LPG gas hoses embodies a blend of technical prowess, stringent safety standards, and insightful market expertise. At the forefront of this industry are factories that have mastered the art and science of seamless production, ensuring safety, durability, and efficiency in their products.
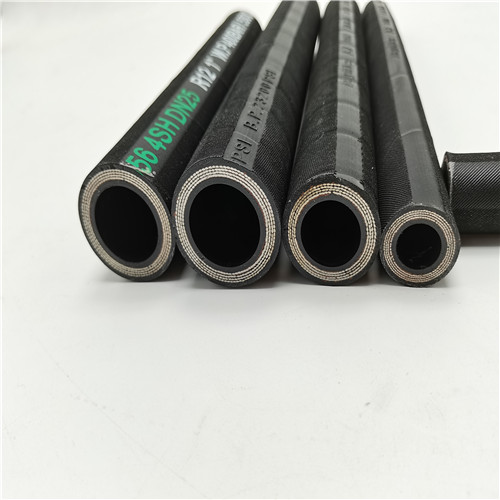
Factories specializing in LNG gas hose manufacturing operate under the paramount principle of safety. Given the critical nature of their application—namely the transfer of liquefied petroleum gases from storage tanks to consumers—these hoses are designed and produced to withstand extreme conditions. Advanced factories employ a combination of synthetic rubber and thermoplastics to engineer hoses that are flexible yet robust, capable of resisting high pressures and temperatures. The materials are meticulously selected to prevent wear and tear caused by the abrasive nature of LPG.
Expertise in the field of LPG gas hose manufacturing doesn't solely rest on material science. Leading factories distinguish themselves through their R&D departments, which are tasked with innovative solutions that anticipate and exceed regulatory requirements. The involvement of skilled engineers in designing hoses that incorporate cutting-edge polymer technology illustrates how these factories not only adhere to but often establish industry benchmarks. The deployment of computer-aided design (CAD) software ensures precision, allowing for the customization of products that meet specific consumer needs.
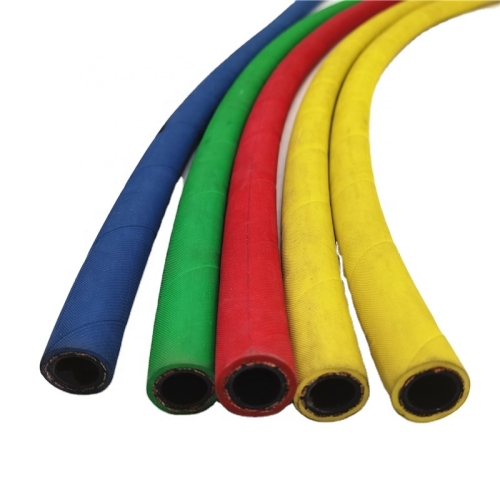
A notable factor contributing to a factory's authoritativeness in this domain is its rigorous testing protocols. Adhering to international standards such as the ISO 2928, respected factories do not compromise on validating the strength and flexibility of their hoses. This involves exposure to a battery of tests that simulate extreme operational environments, from fluctuating temperatures to potential exposure to harsh chemicals. Such comprehensive testing guarantees that the end products not only meet the statutory regulations but often exceed them, earning trust on both a commercial and consumer level.
lpg gas hose factories
The credibility of an LPG gas hose factory is further enhanced by its commitment to environmental and ethical standards. Modern factories are increasingly adopting greener manufacturing practices, reducing emissions and decreasing energy consumption during production. They engage in sustainable sourcing of materials, thereby minimizing the environmental footprint. This commitment extends to ethical labor practices, ensuring worker safety and promoting a culture of transparency and accountability.
Building trust among distributors and end-users is an integral part of the reputation of a leading LPG gas hose factory. This is accomplished through transparent communication regarding product capabilities and limitations, fostering an environment where consumers are well-informed about safe use practices. Additionally, responsive after-sales service contributes significantly to customer satisfaction, which is often a decisive factor for repeat business in this otherwise competitive industry.
Ultimately, the expertise and trustworthiness exhibited by top-tier LPG gas hose manufacturers pivot around their ability to blend technology and innovation with a steadfast commitment to quality and safety. By consistently raising the bar for performance standards, product reliability, and customer service, these factories not only sustain but drive the growth of the LPG gas market, solidifying their position as industry leaders. The fusion of state-of-the-art technology, responsible manufacturing practices, and superior customer relations set these factories apart, providing a template for success that few can replicate.