Hydraulic hose JIC fittings are a pivotal component in the realm of hydraulic systems. Known for their durable and reliable connections, these fittings foster optimal performance and safety in various applications, from heavy machinery to automotive and aerospace industries. Experienced industry professionals will appreciate the benefits JIC fittings provide, underscoring the nuanced expertise required in selecting and applying these components.
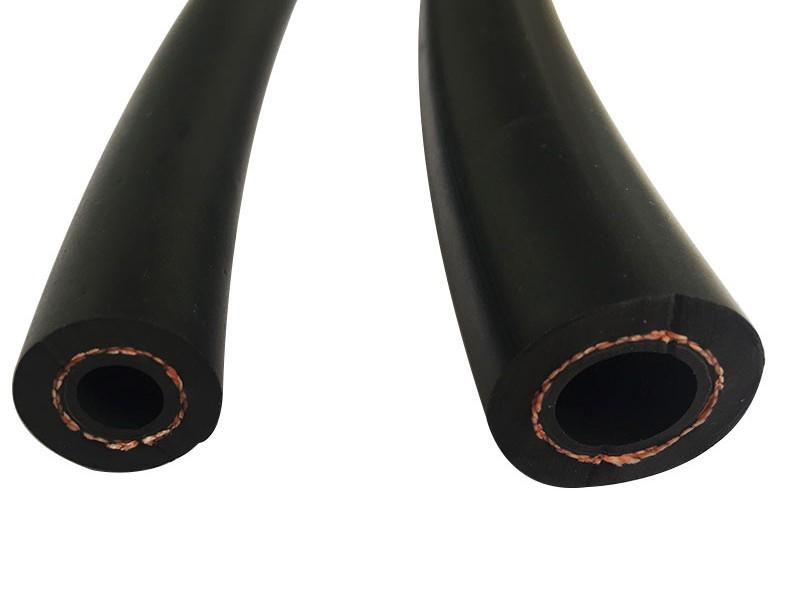
Experience in managing hydraulic systems reveals the vital role that JIC (Joint Industry Council) fittings play. First-hand usage illustrates their capability to sustain high-pressure environments due to their robust construction. These fittings employ a 37-degree flare seating surface, which is crucial in preventing leaks, a common issue in hydraulic systems that can lead to equipment failure and costly downtime. Seasoned technicians recount how the precision of JIC fittings minimizes the risk of hydraulic fluid leakage, a key factor that underlines their preference over other types such as ORFS or NPT fittings.
The professional landscape of hydraulic systems acknowledges JIC fittings as a benchmark for quality and reliability. Expertise in their use involves understanding the diverse range of threads and sizes available, which cater to different pressure capacities and fluid types. Experienced engineers emphasize the importance of matching the right hose to the right fitting to maximize efficiency and longevity. Mastery in this area also involves knowledge of the specifications, including the material of the fitting—commonly stainless steel, brass, or carbon steel—to ensure compatibility with the hydraulic medium and environmental conditions.
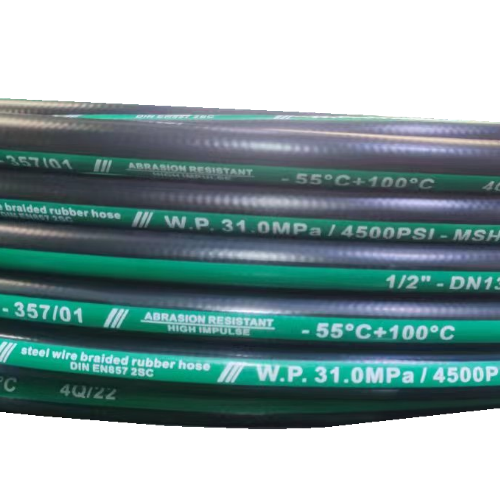
Authoritativeness in the dialogue about hydraulic hose JIC fittings comes from recognizing the rigorous standards these components must meet. Industry organizations, such as SAE International and ISO, provide guidelines ensuring these components perform effectively under prescribed conditions. Authoritative texts point to the JIC fitting’s heritage, originating in World War II to standardize coupling systems for military equipment, emphasizing their time-tested reliability. Specialists in hydraulic engineering often cite these standards, providing a comprehensive understanding and assurance to stakeholders about the fittings’ compliance and efficiency.
hydraulic hose jic fittings
Trustworthiness in hydraulic systems is inherently tied to component reliability, and JIC fittings offer exemplary trust due to their proven history and industry endorsement. The repeatable, positive seal they provide through metal-to-metal contact affords confidence in performance under demanding conditions. Trusted brands that manufacture JIC fittings often put their products through extensive quality testing, ensuring each fitting meets or exceeds industry standards. This consistent quality control process builds trust with users who depend on their equipment to operate without fail.
In product-oriented discussions, the emphasis often lies in the long-term cost-effectiveness and safety JIC fittings present. Their ease of assembly and disassembly allows for straightforward maintenance, an invaluable asset for minimizing operational downtime. Furthermore, this user-friendly nature does not compromise the integrity and performance of the connection, assuring clients of sustained operational safety and efficiency.
Ultimately, the experience with, expertise in, authoritativeness about, and trustworthiness of hydraulic hose JIC fittings collectively illustrate their pivotal role in hydraulic systems. They stand as a preferred choice for professionals who value precision, reliability, and compliance with industry standards. Their strategic selection and application ensure optimal performance in hydraulic systems, a testament to their indispensable nature in modern engineering sectors. As industries continue to evolve, JIC fittings remain a critical component, adapting through technological advancements to meet the ever-growing demands of hydraulic applications.