High temperature hydraulic hoses are a critical component in various industries, providing the means to transfer power efficiently in extreme conditions. Recognized for their robustness and durability, these hoses are crucial for applications that require the transfer of fluids under elevated temperatures. Delving into their importance, technological advancements, and the reasons behind their trusted status in industrial sectors can provide a comprehensive understanding of why they are indispensable.
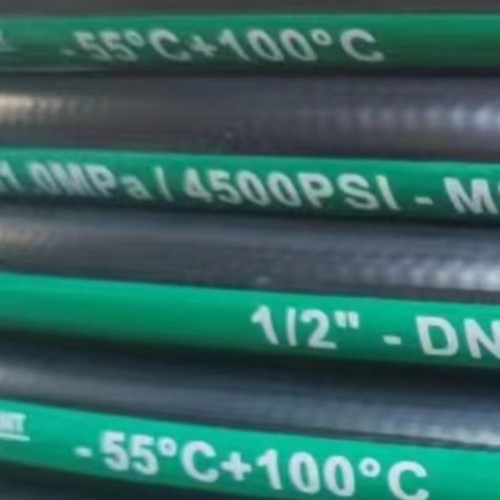
Industries such as manufacturing, mining, and construction rely heavily on hydraulic systems to power machinery and perform demanding tasks. Here, high temperature hydraulic hoses play a pivotal role. Designed to withstand extreme heat, they prevent equipment malfunction and ensure continuous operation even in harsh environments. Their ability to endure temperatures sometimes exceeding 300°F makes them an essential part of operations in steel mills, foundries, and other high-temperature settings.
What sets high temperature hydraulic hoses apart is not just their heat resistance but also their construction and material composition. Typically made from synthetic rubbers like EPDM or Viton, these hoses are reinforced with multiple layers of braided steel or textile. This design not only allows them to resist heat but also provides remarkable flexibility and resilience under pressure. Unlike standard hydraulic hoses, the high-temperature variants incorporate a special heat-resistant cover that shields against external abrasion, chemical exposure, and environmental factors.
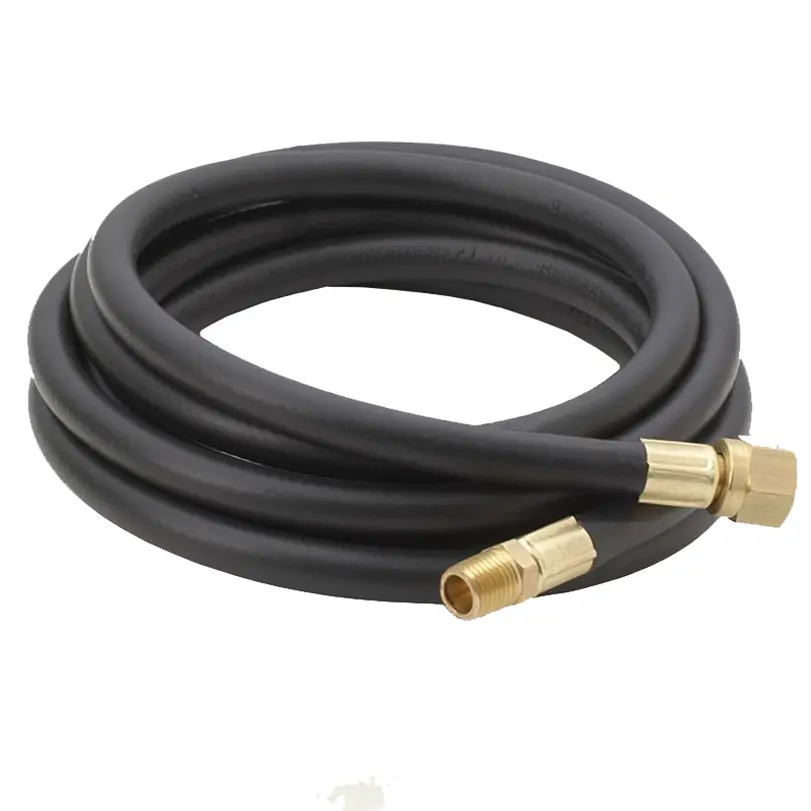
From an engineering perspective, selecting the appropriate high temperature hydraulic hose involves evaluating several factors. These include understanding the system’s pressure requirements, the fluid being conveyed, and the environmental conditions. A hose that excels in these parameters will improve the system's efficiency and longevity. For instance, a hydraulic system operating in a desert environment would benefit significantly from hoses with enhanced UV and ozone resistance in addition to heat resistance.
Technical expertise in the installation and maintenance of these hoses is paramount. Improper installation can lead to premature failure and system breakdowns.
It is advised to engage professionals with extensive training and experience in hydraulic systems. A skilled technician will ensure that the hoses are installed with the correct fittings and bends, minimizing the potential for leaks and mechanical wear.
high temperature hydraulic hose
Moreover, regular maintenance and inspection of high temperature hydraulic hoses cannot be overstated. Over time, even the most robust hoses can succumb to fatigue and wear. Regular checks for signs of abrasion, cracking, or swelling can prevent unexpected failures. Utilizing advanced diagnostic methods like thermographic imaging can help in early detection of potential issues, ensuring timely intervention and repair.
In terms of authority and trust, leading manufacturers in the hydraulic industry like Parker Hannifin, Eaton, and Gates Corporation have long established their reputation through rigorous product testing and quality assurance processes. These companies provide extensive product documentation, certifications, and compliance with international standards such as SAE and ISO, reassuring users of their commitment to safety and performance.
Ultimately, the trustworthiness of high temperature hydraulic hoses stems from their proven track record over decades of use in challenging applications. Businesses invest heavily in training their workforce in the use of these components, often collaborating with manufacturers for specialized training programs. This collaboration ensures that knowledge is up-to-date with the latest technological improvements and industry best practices.
Through years of development and refinement, high temperature hydraulic hoses have embodied qualities that meet the critical needs of industry reliability, durability, and efficiency. Their continued evolution and adaptation to new challenges ensure they remain an indispensable tool in the industrial toolkit, driving progress in environments where few other options suffice.