High pressure hydraulic hoses are critical components in countless industrial applications, where safety, reliability, and performance are paramount. Choosing the right hose isn't just about selecting a product off the shelf; it's about ensuring optimal performance, minimizing downtime, and extending the lifespan of your machinery.
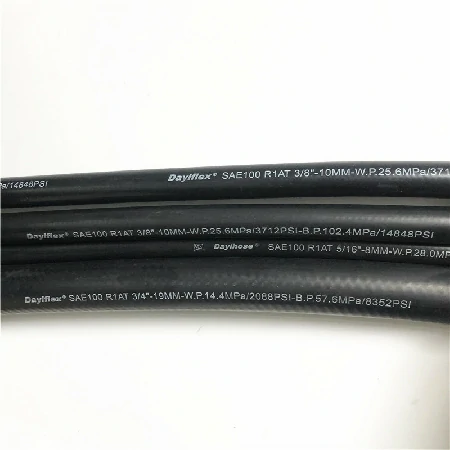
High pressure hydraulic hoses are designed to transmit hydraulic fluid to various hydraulic components, valves, actuators, and tools.
Built to withstand high pressure and temperature extremes, these hoses must be both flexible and durable. Their construction typically involves several layers of reinforcement to handle the demands of pressurized flow and environmental conditions.
The selection of a high pressure hydraulic hose should be guided by four crucial principles compatibility, pressure rating, flexibility, and the environment in which it operates. Compatibility refers to the hose’s ability to withstand the type of fluid being transmitted. It should resist chemical degradation to ensure longevity and safety. Pressure rating is equally vital; the hose must be capable of handling both the working pressure as well as any potential surges. Flexibility is another key factor, as the overall efficiency of hydraulic systems often relies on the hose's ability to navigate complex, tight spaces without kinking or fracturing. Lastly, the environmental considerations such as temperature, ultraviolet exposure, and abrasive surroundings must be factored into the selection process.

A common issue faced by many industries is hydraulic hose failure, which can result in unmet operation needs or, even worse, dangerous accidents. This makes it imperative that operators understand installation procedures and maintenance schedules. For instance, regular inspections should be carried out to detect early signs of wear or damage such as cracks, blisters, or kinks. Worn fittings and connections also need regular checking to prevent leaks.
In practice, high pressure hydraulic hoses are utilized in sectors such as construction, agriculture, and manufacturing, each with its own unique demands. Agricultural settings often involve exposure to chemicals and weather elements that necessitate highly robust hoses. In contrast, construction machinery often requires hoses that are supremely flexible to handle the heavy vibration and dynamic pressure changes.
high pressure hydraulic hose
It's also recommended to leverage products from reputable manufacturers who subject their hydraulic hoses to stringent testing protocols. Quality standards such as SAE, ISO, and EN are reliable indicators of a hose's quality, confirming its ability to perform under specified conditions.
Ultimately, these hoses are an investment, and maximizing their utility is both a science and an art. Professionals recommend keeping a detailed log of each hose's usage, including specific fluids used, the pressure environments encountered, and the frequency of maintenance. This documentation not only aids in troubleshooting but also in making informed decisions when it comes time for replacements.
Working with suppliers who offer comprehensive support, including technical advice and training on latest technologies, further enhances the decision-making process. Technologies like smart hoses fitted with diagnostic sensors are increasingly helping industries predict potential failures and prevent downtime, thus extending the operational life of high pressure hydraulic systems.
To ensure the integrity and performance of your high pressure hydraulic systems, invest in understanding the specific needs of your operation. With the right knowledge and tools, you can significantly enhance the safety and efficiency of your hydraulic applications, securing a more prosperous and productive industrial environment.