The Critical Role of Hoses in Gasoline Production
In the complex and intricate process of gasoline production, hoses play a vital role that is often overlooked. These specialized conduits are not merely passive components; they are integral to the safe and efficient transfer of fluids within gasoline factories. This article delves into the importance of hoses designed for use in these facilities, highlighting their unique features and the significant impact they have on the production process.
Hoses for gasoline factories are engineered to withstand the rigorous demands of industrial environments where volatile liquids such as gasoline are handled. They are typically made from materials that can resist chemical degradation, such as synthetic rubber or thermoplastic compounds. These materials offer excellent resistance to oils, fuels, and other petroleum products, ensuring that the integrity of the hose remains intact despite continuous exposure.
Furthermore, hoses used in this context are built to manage high pressures without compromising their structural stability. The high-pressure resistance is crucial during the pumping and transport of gasoline, where any leak or failure can lead to severe safety hazards and environmental contamination. Therefore, manufacturers of these hoses adhere to strict quality standards and performance tests to guarantee their reliability under stress.
The design of hoses for gasoline factories also includes features such as reinforced layers and burst resistance. Reinforcement ensures that the hose maintains its shape and strength over time, while the ability to resist bursting under extreme conditions protects against catastrophic failures Reinforcement ensures that the hose maintains its shape and strength over time, while the ability to resist bursting under extreme conditions protects against catastrophic failures
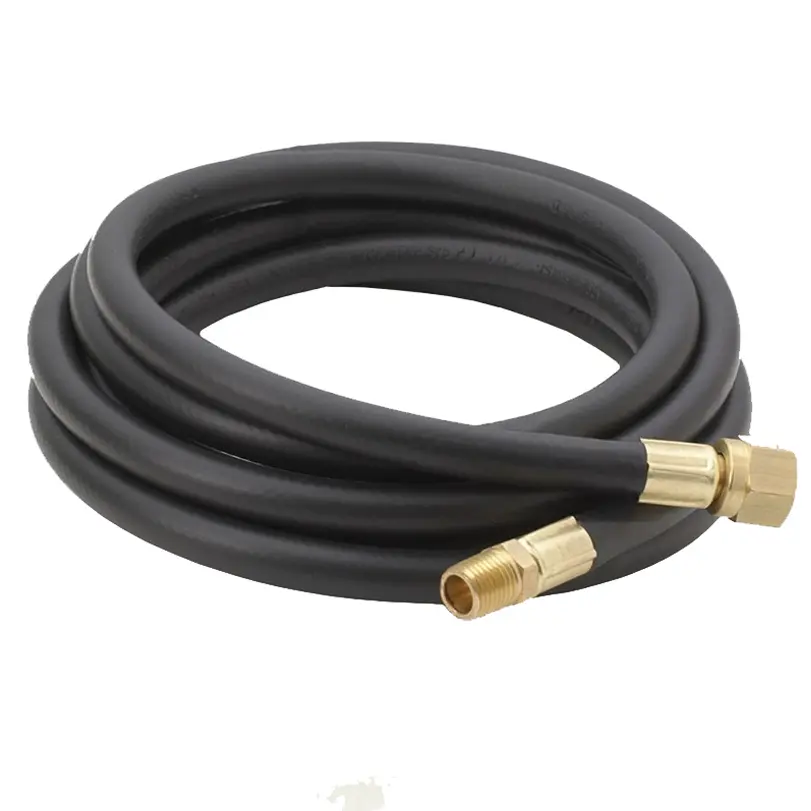
Reinforcement ensures that the hose maintains its shape and strength over time, while the ability to resist bursting under extreme conditions protects against catastrophic failures Reinforcement ensures that the hose maintains its shape and strength over time, while the ability to resist bursting under extreme conditions protects against catastrophic failures
hose for gasoline factories. Additionally, many hoses are equipped with fittings and connectors that provide secure attachment points, preventing leakage at joints and promoting a seamless transfer of fluids.
In terms of application, hoses are utilized throughout various stages of gasoline production. They transport raw materials to distillation columns, move intermediate products between processing units, and convey the finished gasoline to storage tanks. Each step requires precise control over flow rates and volumes, and hoses must be capable of adapting to these requirements with minimal maintenance.
Moreover, hoses contribute to environmental stewardship by minimizing spills and evaporative losses. With their robust construction and tight seals, they help contain gasoline within the closed system of the factory, reducing the risk of harmful chemicals escaping into the surrounding ecosystem.
In conclusion, hoses for gasoline factories are specialized tools that ensure the smooth operation of these facilities. Their chemical resistance, high-pressure handling capabilities, and reliable designs make them essential components in the production of gasoline. As technology advances, it is likely that these hoses will continue to evolve, enhancing their performance and further supporting the critical work of gasoline factories around the world.