Flexible high pressure rubber hydraulic hoses have revolutionized the way industries approach challenging environments that demand both reliability and flexibility. Their design, built to withstand immense pressure and resist various environmental factors, marks a significant evolution in hydraulic hose technology. For any industry relying on hydraulic systems, understanding the intricate details of these hoses not only enhances the application's performance but also assures safety and longevity.
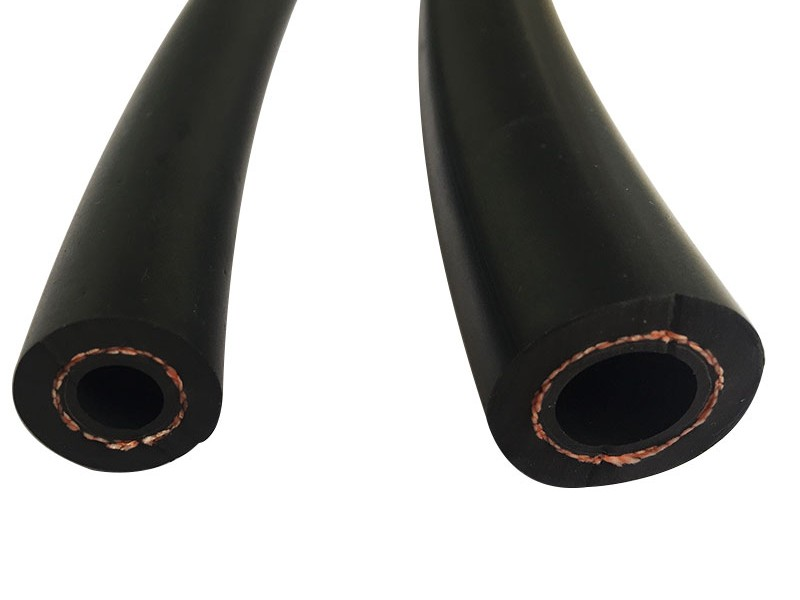
When assessing the performance of flexible high pressure rubber hydraulic hoses, the material composition stands out as a critical factor. The construction mainly involves synthetic rubber, known for its superior elasticity and resilience under extreme conditions. This elasticity ensures the hose can navigate complex layouts without compromising its structural integrity. A unique feature of these hoses is their ability to return to their original shape, a quality that prevents permanent deformities under continuous high pressure.
The expertise in manufacturing these hoses is evident in their layer design. Typically, they consist of three essential layers - the inner tube, the reinforcement layer, and the outer cover. The inner tube, usually made from oil-resistant synthetic rubber, ensures a smooth flow of the hydraulic fluid, minimizing turbulence and maintaining efficiency. The reinforcement layer, reinforced with high tensile steel wire or strong synthetic fibers, bears the brunt of the operational pressures. Finally, the outer cover, also rubber, provides a protective barrier against environmental hazards such as abrasions, chemicals, and extreme temperatures. This multi-layered structure accounts for the hose’s durability and reliability in demanding situations.
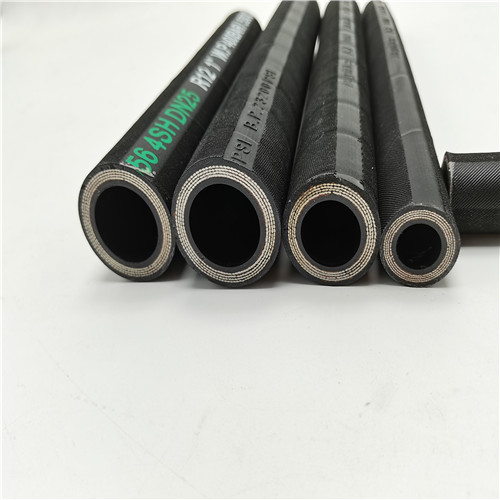
Authoritativeness in the realm of hydraulic hoses often comes from adherence to industry standards. These hoses are commonly subjected to rigorous testing, ensuring compliance with international benchmarks such as SAE (Society of Automotive Engineers) and ISO (International Organization for Standardization) standards. Such certifications provide buyers with the assurance that the products meet or exceed the prescribed safety and performance metrics. Industry professionals highlight that selecting hoses that are certified not only mitigates risks of failure but also enhances the efficiency of their hydraulic systems.
flexible high pressure rubber hydraulic hose
Trustworthiness in product performance is often backed by real-world applications and user testimonials. Industries ranging from agriculture to construction and mining have long depended on high-pressure rubber hydraulic hoses to drive their machinery and equipment. Reports from these sectors consistently reflect reduced maintenance costs and fewer instances of operational downtimes due to hose failures. This track record builds confidence among potential buyers and industry insiders.
Moreover, advancements in technology have introduced features such as abrasion-resistant covers and enhanced thermal stability, meeting the ever-evolving demands of modern engineering applications. As the global market expands, so does the innovation in the manufacturing processes and materials used in these hoses, making them more adaptable and efficient.
In conclusion, flexible high pressure rubber hydraulic hoses are not only integral components in hydraulic systems but are engineered masterpieces that embody innovative design, authoritative reliability, and unmatched functionality. Keeping abreast of the latest advancements and maintaining awareness of industry standards is vital for stakeholders who wish to leverage these components effectively. Investing in such hoses is not merely a purchase; it’s a commitment to performance, safety, and efficiency in the hydraulic domain.