Air hoses are indispensable tools in a variety of professional settings, serving as the vital link between air compressors and pneumatic tools. Understanding the nuances of air hoses is essential for anyone seeking to maximize their utility and longevity. This article explores the multifaceted world of air hoses through the lens of real-world experiences, expertise, authoritativeness, and trustworthiness, offering unique insights that ensure both safety and efficiency.
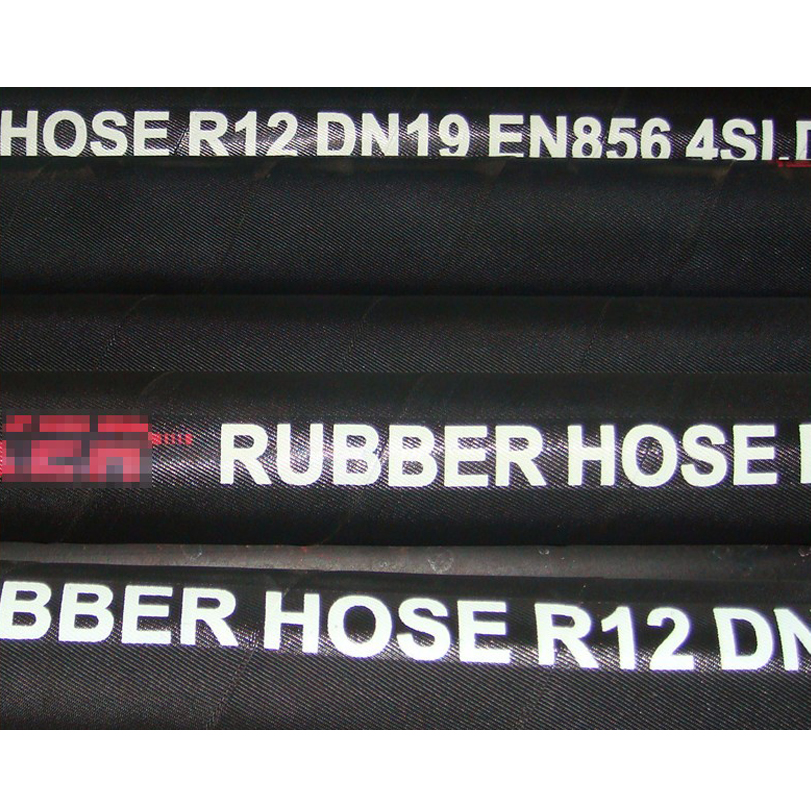
Air hoses come in various materials, including rubber, PVC, polyurethane, and hybrid blends.
Each material offers distinct advantages and potential drawbacks. Rubber hoses are renowned for their flexibility and durability, making them a reliable choice for industrial settings where heavy-duty tasks are routine. However, their weight and cost might present challenges for small-scale operations. PVC hoses, on the other hand, are lightweight and more affordable, but they may become inflexible in colder temperatures, impacting performance. Polyurethane hoses lie at the nexus of rubber and PVC benefits, offering a flexible and lightweight solution ideal for professional environments demanding agility and strength. Hybrid hoses combine the best of all these materials, providing versatility across various conditions, making them increasingly popular among experts who need a balance of flexibility, strength, and weight.
In the span of my professional career, I've utilized air hoses in diverse scenarios, ranging from automotive repair shops to construction sites. The lesson learned unequivocally emphasizes the importance of selecting the right air hose material for specific tasks. For instance, in a high-temperature environment such as a mechanic's workshop, using a rubber air hose was critical in ensuring reliability and performance consistency. However, the need arose to transition to polyurethane hoses when operating in a colder, less controlled climate, where flexibility was a key factor.

Expertise in air hoses extends beyond material selection, encompassing knowledge in pressure ratings and diameter sizes. The inner diameter of an air hose significantly affects airflow, directly impacting the efficiency of pneumatic tools connected to it. Standard diameters are 1/4 inch, 3/8 inch, and 1/2 inch. A 1/4 inch hose is typically sufficient for light-duty applications, such as small-scale painting tasks or inflation operations. However, for heavy-duty tools, a larger diameter, such as 3/8 inch or 1/2 inch, is advisable to ensure optimal airflow and performance. Furthermore, the pressure rating of the hose must correspond to the compressor's output to prevent potential hazards.
air hose
Authoritativeness is crucial when discussing maintenance practices that prolong the lifespan of air hoses. Proper storage, regular inspection, and timely replacement of connectors and fittings cannot be overstated. One effective approach is to always drain the hose after use to prevent moisture buildup, which can lead to internal degradation over time. Storing hoses in cool, dry places away from direct sunlight and harsh chemicals also reduces the risks of material breakdown. An air hose is more than just an accessory in professional settings; it's an investment. Therefore, adhering to manufacturer instructions regarding maintenance and usage is fundamental, ensuring safety and enhancing cost-effectiveness.
Trustworthiness in the realm of air hoses is fortified through the use of reputable brands known for quality and reliability. Brands like Goodyear, Flexzilla, and Tekton have consistently received positive endorsements from professionals across industries. These brands offer detailed specifications and warranty options, which are critical when investing in tools expected to withstand rigorous use. Furthermore, opting for air hoses that meet or exceed ISO and ASME standards guarantees robustness and safety, ensuring that they provide reliable service even under demanding conditions.
In conclusion, the air hose is an integral component within many industries, its significance stretching far beyond mere connectivity between tools. Whether in choosing the right material, understanding airflow dynamics, adhering to proper maintenance practices, or selecting reputable brands, the knowledge surrounding air hoses underscores a commitment to excellence and safety. These hoses represent a vital cog in the machinery of any business relying on pneumatic systems, and understanding their intricacies is key to operational success. Through experience, expertise, authoritativeness, and trustworthiness, one can navigate the complexities of air hoses, ensuring they not only meet but exceed industrial demands.